ERP System Cost
The Real ERP Price for implementing an ERP System and what needs to be budgeted for.
7/13/20254 min read
ERP systems represent a significant investment for any organisation. The price tag attached to the software is only the starting point. Many businesses underestimate what it takes to keep an ERP system running effectively and aligned with ongoing operational needs.
A thorough financial assessment should consider not only the initial implementation but also the ongoing costs required for business-as-usual operations.
An effective ERP business case must separate costs into two categories:
Implementation Costs — required to get the system live and operational.
BAU Costs — required to sustain ongoing operations and continuous improvements.
Excluding BAU costs from financial planning creates risk for future budget overruns and operational strain. A complete view of costs ensures alignment between technology investment and business strategy. Organisations planning ERP projects should insist on compiling the detailed cost breakdowns and challenge assumptions early to secure successful outcomes. A summary of typical costs are listed in the table below.
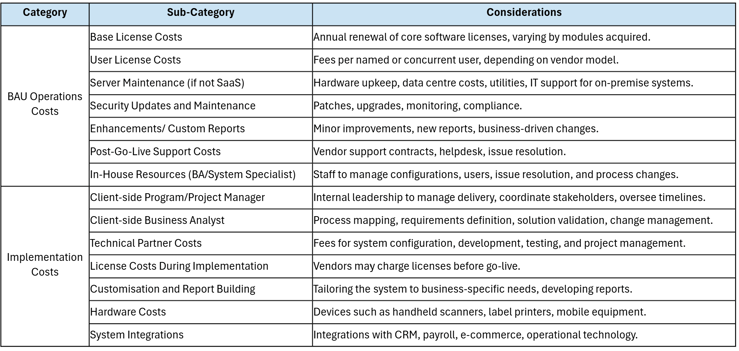
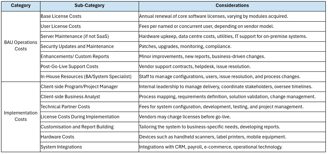
Successful ERP implementations require dedicated roles on the client side to ensure that the system meets business needs, stakeholders remain aligned, and the project remains under control. Two roles stand out as critical: the Business Analyst (BA) and the Project/Program Manager (PM).
ERP Project/Program Manager (PM)
A client-side PM is a non-negotiable requirement for any ERP implementation. This is a temporary role, focused on guiding the project from business case development through to the conclusion of the hyper-care period following go-live. Many projects fail or experience significant cost overruns when project management responsibilities are assigned to internal subject matter experts who are already involved in business-as-usual operations. While SMEs hold critical operational knowledge, they often lack the structured project management expertise necessary to navigate the complexities of ERP implementations.
A dedicated PM brings:
Formal project governance and structure, ensuring all project phases are planned and controlled.
Risk identification and mitigation, reducing the likelihood of unexpected issues derailing timelines or budgets.
Stakeholder coordination across business units and external partners, keeping communication clear and actions aligned.
Scope management, preventing uncontrolled changes that inflate costs and timelines.
The structured approach provided by an experienced PM transforms the ERP project from a set of disconnected tasks into an organised program of work. This is what enables the project to take shape and achieve its objectives, rather than relying solely on general ERP knowledge or operational expertise. While the implementation partner will typically have a PM, their role is entirely focused on managing their technical resources and is typically focused on maximising their firm's profitability rather than managing client-side resources, scope and costs.
ERP Consultant / Business Analyst
The necessity of a client-side BA often depends on the size of the organisation and the complexity of the ERP platform selected. For smaller businesses deploying a relatively basic ERP solution, ongoing support and minor system changes might be more cost-effective when outsourced to a support partner. However, in medium and large-scale deployments, or where significant business process change is expected, a client-side BA provides significant value.
A BA performs the following crucial functions:
Translates business processes into system requirements, ensuring the ERP solution reflects real operational needs.
Supports with master data governance and cleaning up data.
Reviews configurations and customisations delivered by technical partners, validating that solutions align with the intended business outcomes.
Develops and executes test scenarios based on business use cases, safeguarding business operations during transition.
Supports change management activities by helping end-users understand and adopt the new system.
In small organisations, an experienced PM may fill in this role during the implementation phase and then hand over the support function to the outsourced support partner.
Implementation Vendor / Technical Partner
An implementation vendor is a specialised partner engaged to deliver technical and functional services required to deploy an ERP system. This partner possesses in-depth expertise with the selected ERP platform and provides resources who understand both the software and the methodologies needed to configure it effectively for different business environments.
Typical responsibilities include:
Running design workshops and translating business needs into system configurations
Customising the ERP, building reports, and managing integrations
Migrating data and setting up technical environments
Supporting testing and training activities
Providing hyper-care support after go-live
License Costs
License costs for an ERP system typically include a base module fee and additional user license fees. User licenses follow one of two models:
Named User Licenses: Assigned to specific individuals and generally remain fixed unless users leave or change roles.
Concurrent User Licenses: Operate as a pool, allowing a set number of users to be logged in at the same time, regardless of who they are.
Understanding the license model is crucial for estimating costs accurately and aligning licenses with operational needs.
System Integrations, Customisations and Reporting in ERP
Minor customisations are common during ERP implementations to ensure the system fits unique business processes. Each customisation should be carefully assessed to confirm it’s truly necessary, as excessive changes can increase cost and complexity.
Additional reports and custom templates, such as invoices or purchase orders, often need to be developed because standard ERP outputs may not fully meet business or regulatory requirements. Balancing customisation needs against cost and long-term supportability is critical for a successful implementation.
System integrations are another key cost area. Connecting the ERP to other systems like HRIS, Payroll, e-commerce, or production equipment ensures smooth data flow across the business but often involves significant technical effort and expense. Costs associated with middleware may need to be considered.
Hardware Considerations in ERP
Hardware needs for an ERP system vary by organisation and industry. In warehouse environments, devices like barcode scanners and label printers are often required to support tasks such as goods receipt, inventory movements, and shipping. On the shop floor, employees may need access to PCs or mobile devices to interact with the ERP system for data entry and operational updates. These locations should also have internet connectivity. The costs associated with implementing this hardware need to be factored in.
Final Thoughts
Exact costs for ERP implementations vary widely based on business size, system complexity, and requirements. As a general guide, small-scale, simple ERP implementations often fall between A$400,000 and A$700,000. A more complex implementation would typically range from A$700,000 to A$2,000,000.
These figures cover both implementation services and associated costs such as licences, hardware, implementation vendor and client-side PM costs.